Materials efficiency and recycling
We continue to make progress against all our key metrics. The average amount of crushed road waste or recycled asphalt planings (RAP) used in new asphalt mixes remained above our 10% target for the third successive year.
Mixing RAP into asphalt makes sense for customers, the environment and the business. It means less virgin aggregate and bitumen are needed, and waste to landfill is reduced, though there is a trade-off between the use of more recycled asphalt and energy consumption. The UK specification allows up to 50 per cent RAP in various asphalt products and we continue to develop new techniques to increase the content in our mixes.
The cement replacement Regen is manufactured from granulated blast furnace slag, a by-product of the steel industry. It reduces embodied CO2 in concrete and provides a number of other benefits. Its use in ready-mixed concrete means we have one of the highest cement replacement rates in the UK market. However, the average amount of Regen used in ready-mixed concrete fell to 36.7 per cent, reflecting a fall in cementitious replacements experienced across the industry over recent years. We believe this is due to changes in market demand, regional variations and a lack of customer awareness.
We continue to develop new concrete mixes with higher Regen content and communicate the CO2 benefits of these products to customers and specifiers through both our marketing programmes and a national programme of CPD courses focused on the ‘Benefits of cement substitutes’. As the carbon costs of cement increase over next few years we plan to maximise Regen content in our concrete, which in turn will create a lower embodied carbon figure for the end user.
The use of alternative raw materials in cement increased to 12.1 per cent – the second highest on record. This included the introduction of 8,500 tonnes of fly ash at Ketton and an additional 10,000 tonnes of shale across the three plants. There were also small increases in production of recycled aggregates and concrete containing recycled materials.
All our concrete plants are recovering at least half of their process waste, surpassing our 2020 target of 95 per cent.
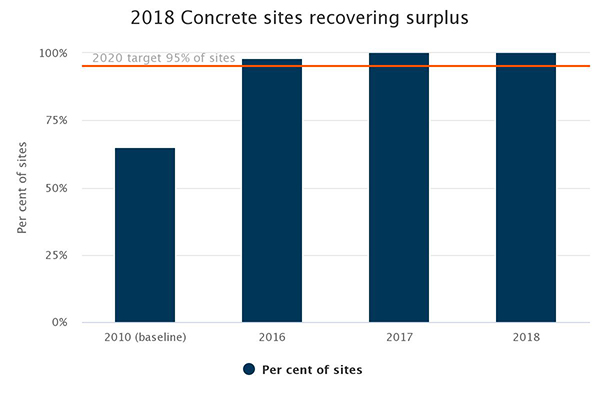
-
Recycled and secondary materials
2010 (baseline)
2016
2017
2018 Definition
By-products or waste used as raw material in cement
8.0%
12.2%
11.5%
12.1% Alternative materials as a % of total cement production
Aggregates recycled and sold
1.77%
0.19%
0.01%
0.14% % of total sales
Recycled materials in asphalt (Hanson plants)
2.9%
11.1%
10.5%
11.0% % of recycled asphalt planings and foundry sand used in asphalt
Recycled materials in asphalt (MQP plants)
19.3%
22.9%
21.4% % of recycled asphalt planings and foundry sand used in asphalt
Recycled materials in concrete
0.08%
0.22%
0.11%
0.21% % of recycled aggregate used in ready-mixed concrete
Sites which recover surplus concrete
65%
98%
100%
100% Sites recovering over 50% of process waste (inc third party recycling)
Cement replacements in concrete (Regen, PFA)
38.4%
38.9%
38.3%
36.7% % of cement substitutes in ready-mixed concrete